Produced Foam Testing
Why is produced foam testing necessary?
Produced foam is tested to determine whether a foam system’s proportioning and induction equipment is accurate and fit for purpose.
While foam proportioning systems are reliable, they should be rigorously maintained and inspected. Regular produced foam testing helps ensure they remain correctly proportioned.
The report you’ll get from our laboratory team will show the calculated percentage induction of your sample when measured against internationally recognised standards NFPA 11:2021 and BS EN 13565-1:2019.
We test all major foam types including, but not limited to:
- AFFF
- AR-AFFF
- HI-EX
- Class A
- FFF
- FP
- FFFP
- AR-FFFP
Please contact us if you’re unsure of your foam type or need any help with shipping.
How to get your Produced Foam tested
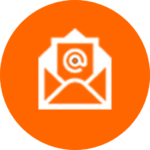
Step 1: Choose your testing & service level
Contact us to tell us what kind of testing and what level of service you require.
For produced foam testing we offer two levels of service:
- Standard Service: 5-working days turnaround from receipt of sample.
- Express Service: 24-hour turnaround from receipt of sample (subject to availability).
Step 2: Collect your sample
For each produced foam test, we require the following samples:
- Foam concentrate: 1 litre
- Produced foam: 1 litre
- Induction water: 1 litre
Samples should be sent in clean, sealed, clearly labelled plastic bottles.
Step 3: Label your samples
To make sure we are testing the correct foam and checking against the relevant parameters, we need certain information to be included on your samples, for example foam type, sample location and foam concentration (%).
Examples can be seen here:
Blank templates can be downloaded from here.
Step 5: Print a Safety Data Sheet
Include a copy of the manufacturer’s safety data sheet along with your sample, if you have one.
If you don’t have an SDS, make sure you include the foam manufacturer’s name on your sample. Please note inclusion of an SDS is usually a shipping requirement.
Step 6: Package & Send
Package your labelled sample, Foam Testing Request Form and Safety Data Sheet, if available, in a suitable box or container and send it to us.
An address label template can be downloaded from here.
Need help with shipping? Contact us for more information.
Step 7: Testing & Report
On receipt of your sample, we’ll get to work testing your foam.
We operate a standard 5-working day turnaround or offer an express 24-hour service (subject to availability): if you’re not sure what you need, contact us. Your report will be emailed to you.
A copy of these steps including a checklist to help make sure nothing has been missed can be downloaded from here.
Other Test Services Available
Foam Concentrate Testing
Evaluates whether your stored foam is in a satisfactory condition and remains compliant with international standards.
IMO Foam Testing
Required to be done by many maritime administrations and bodies on foam stored on board ships in international waters.
PFAS Top Assay Testing
Determines PFAS levels of foam stock and detects any residual PFAS contamination in tanks and equipment.